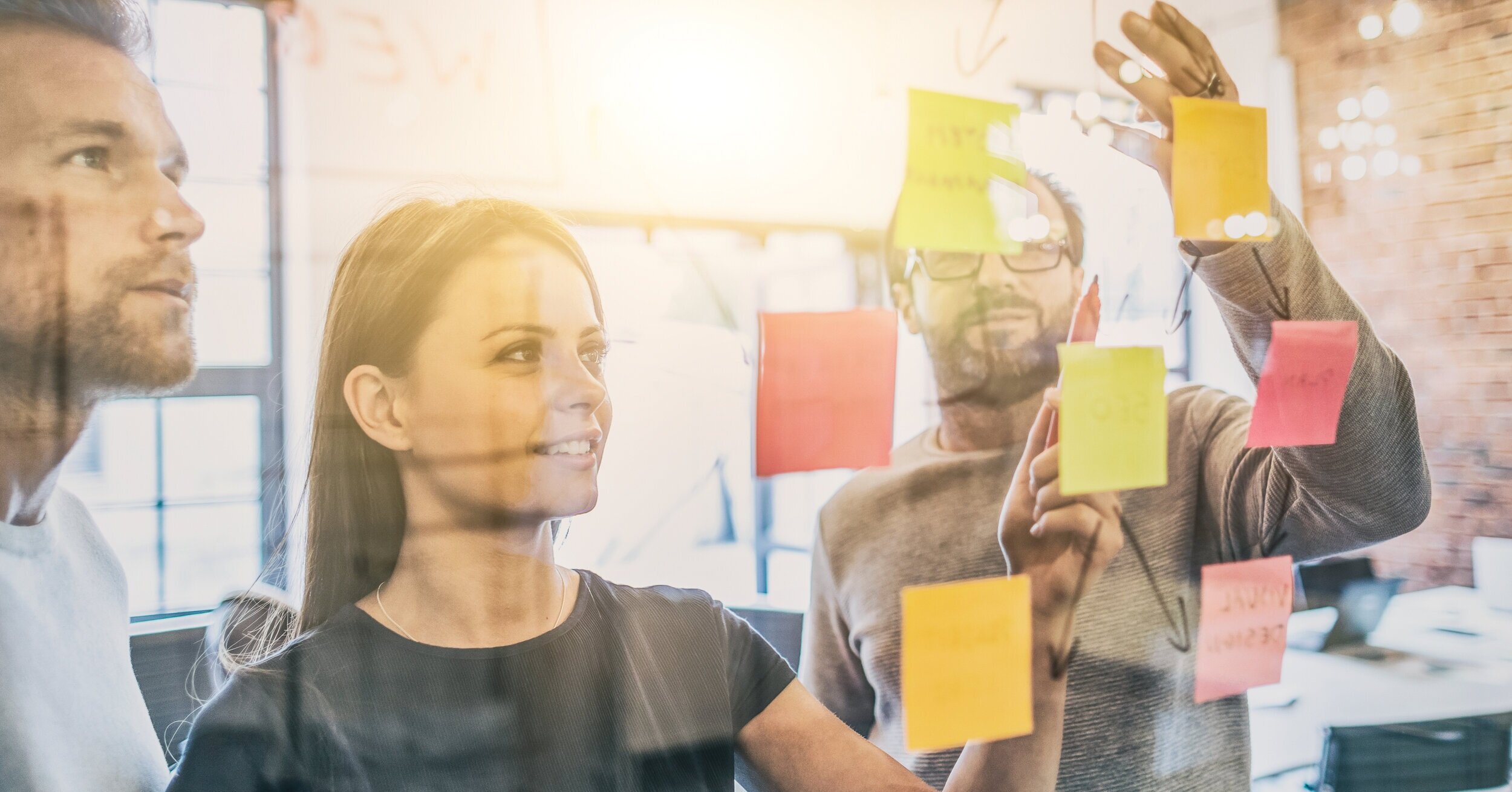
Process Reengineering
Background.
The Organization and Problem Statement
Due to COVID-19 and the resulting quarantine loss of income for many families, the food bank sought to quickly scale up its services to meet the sharp increase in community food insecurity. The sudden demand placed stress on the processes used by the food bank, many of which had evolved to fill performance gaps or address an immediate need. Being a non-profit, the food bank resources focused on meeting the mission rather than designing the organizational infrastructure. As a result, the processes lacked a systemic approach allowing obstacles to arise in the food flow process. As staff and resources reached capacity, they remained committed to the mission.
The Opportunity
Together with Dr. Steve Villachica and Dr. Rob Anson, the team provided consulting and facilitation services to the food bank. Our goal was to systematically assess current processes, identify pain points, and create solutions to alleviate those pain points. The team sought to intentionally design a systemic process to align all stakeholders, efforts, and resources toward meeting the community's needs.
Desired Outcomes
A successful redesign will allow food to flow effortlessly as the needs of the community ebb and flow. This nimble response will in turn afford the food bank the capacity to participate in new programs and opportunities.
Stakeholders.
Workshop participants examined the Distribution Process from the point of view of those who benefit or are impacted by it (Table 1). By naming the success criteria for each stakeholder, they developed empathy for everyone involved and gained an understanding of the purpose behind the process.
Table 1. Food Bank Stakeholders and Their Success Criteria
Process Reengineering Method.
The Process Management Lab (PML), which was founded by the team that conducted the process reengineering project, employed a 2-workshop method to process analysis. In the first workshop, stakeholders and hands-on workers visualized their current (As-Is) processes and identified pain points, and in the second workshop, they integrated prioritized solutions into improved and intentionally designed (To-Be) processes.
The PML facilitated the workshops using video conferencing and online collaborative whiteboard space. The participants agreed to “Playground Rules” (rules of conduct) including confidentiality, space for good and bad ideas alike, and “working the problem” rather than laying blame or finger-pointing.
Differentiator
This approach combines Business and Information Systems models together with Human Performance Improvement models to both increase the flow of products and information and improve the performance of the workers. It seeks to achieve process efficiency and efficacy by assessing processes systemically while considering how individual performers relate to the work processes.
The Current State
(As-Is)
The participants drafted specifications of the process’s stakeholders and their success criteria, process maps (diagrams), then identified major controls for the process and process disconnects/pain points. The PML edited these workshop materials to create an As-Is Report. The workshop participants reviewed the report prior to the next workshop.
The Desired State
(To-Be)
Participants reviewed the process maps from the As-Is workshop and their associated disconnects for accuracy. Participants then prioritized disconnects (pain points), brainstormed solutions, and rated the benefit of implementing the idea, along with the difficulty of doing so, on a scale of High/Med/Low.
The Implementation Plan
Participants generated ideas for implementing the prioritized solutions and specified the potential impact of each implementation idea using the following attributes:
Safety
Correct Quantity (Order to Pick Accuracy) – if not able to deliver requested items, consult with the customer
Correct Place (Delivery Location)
Correct Time (Delivery Window)
Minimize Errors/Rework (Inventory Accuracy)
Reduce Customer Complaints (Complaint Logging by Partner Agencies)
Conclusion.
The reengineering workshops themselves, the mere act of bringing the stakeholders together, affected a change in worker morale. Using video conferencing, everyone had equal access and equal say, including those who were at remote branches or pantries. Prioritizing problems and solutions by anonymous vote allowed all voices to be heard without fear of retaliation for going against the crowd. Overwhelmingly, voting declared the following top two solutions to be most viable (and desirable) for implementation. The process improvement recommendations were presented to the Food Bank leadership (Mammenga, et. al., 2021).
Use technology to automate Food Bank Distribution components.
Information Flow: Much of the food distribution process relies on manual operations and paper-based forms to communicate orders, create pick lists, and coordinate deliveries with agencies.
Real-time Product Tracking: A combination of hardware and software such as a Warehouse Management System (WMS) can automate updates to inventory control through the use of barcode scanners and location verification to reduce errors and improve delivery efficiency.
The Human Factor: The high number of participant votes associated with this solution indicates overall team readiness to implement and adopt technologies.
Ideas for Solution Implementation
Requires money and IT resources. Need to involve leadership and finance.
Work with other food banks to understand their technology and how they use it.
System reliability needs to be high (and have a Plan B for when technology breaks down).
Take the time to provide training and get warehouse buy-in.
The COVID-19 pivot was draining. Beware of change fatigue on staff when adding new technology.
Employ an integrated approach for performance improvement.
Isolated improvement measures tend to have limited impacts on performance. For sustained and meaningful improvement, bundle together multiple activities. Initial steps usually involve:
Specifying metrics to track attainment of performance goals.
Creating instructions in the forms of SOPs, job aids, and training.
Planning for some practical assessment of attainment (a.k.a. “mastery testing” of job task performance).
Providing follow-up and accountability from management, including coaching and feedback.
Ideas for Solution Implementation
Get partner agency agreement that they need more training about delivery windows. Create easy-to-follow printable instructions and send them to partners.
Determine cross-train agenda; schedule training time; document completion. Create a practical evaluation. Make sure the warehouse staff is cross-trained. Immediate impact--if there are problems the driver will tell them.
Make time in the daily schedule to complete the (random) spot checks of food temp (audit-ready at all times). Involve warehouse lead (etc.) and involve all warehouse staff in spot checks. Add recognition program.
Schedule training time; document completion. Determine frequency (i.e. 3x per week) and document for accountability; determine how many correct findings result in not needing to spot check anymore.
References.
Garrido-López, M., & Hillon, Y. C. (2020). Where are the people in continuous improvement efforts? Institut De Socio-Économie Des Entreprises Et Des Organisations (Écully, Rhône).Recherches En Sciences De Gestion, (138), 101-130. Retrieved from https://libproxy.boisestate.edu/login?url=https://www-proquest-com.libproxy.boisestate.edu/scholarly-journals/where-arepeople-continuous-improvement-efforts/docview/2444521903/se-2?accountid=9649
Habib, M. N. (2013). Understanding critical success and failure factors of business process reengineering. International Review of Management and Business Research, 2(1), 1-10. https://tarjomefa.com/wp-content/uploads/2016/07/4722-English.pdf
Mammenga, J., Anson, R., & Villchica, S. (2021). To-be process documentation process: Last mile distribution (LMD). Unpublished manuscript.
Rummler-Brache Group. (2020, October 14). Process relationship map. RummlerBrache Group. Retrieved May 12, 2021, from https://www.rummlerbrache.com/process-improvement-mapping-tools.